https://meet.google.com/phz-aucp-ucb?authuser=0Drilling may seem like a purely Earth-based activity – used to search for oil, install geothermal heating systems, or study soil mechanics. But in space science, it’s fast becoming a crucial part of exploring other celestial bodies, from the lunar surface to the Martian surface, and even distant asteroids.
Understanding the drilling process in space is key to unlocking off-Earth resources that could support future settlements and missions. Let’s break down why we drill, how we do it, and what’s coming next.
Why Do We Need to Drill in Space?
Just like on Earth, there are many reasons we might want to drill on planetary bodies and extraterrestrial bodies. Some are scientific: collecting rock samples or core samples from beneath the surface helps us study the history and geology of other worlds. Others are practical – space advocates and engineers are increasingly interested in drilling for construction, resource extraction, and even future heating solutions.
Could we someday use geothermal heating on the Moon or Mars? Possibly. But for now, the main goal is prospecting. This means finding useful resources, such as metals, ice, or volatiles, that can support space mining or human exploration.
In planetary exploration on Earth, drilling follows a phased approach. First, wide-grid drilling finds a potential ore body. Then, tighter-grid drilling helps define the size, shape, and richness of the deposit. The same strategy will likely apply to the Moon and Mars. However, with asteroids, it’s different: due to their formation, metals tend to be evenly spread. So, only limited drilling may be needed to confirm what’s there.
Drilling Techniques Used in Space Missions
Drilling on other worlds isn’t as simple as dropping a drill string and switching on the engine. Each mission faces different environmental conditions – from low gravity to abrasive dust and extreme cold, which require specialized drilling techniques. Let’s take a look at how various missions have tackled it so far!
The Moon
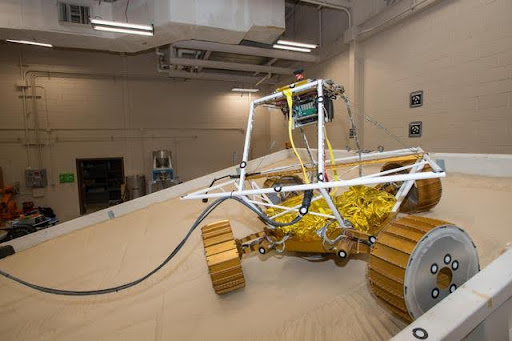
NASA’s upcoming VIPER rover and Intuitive Machines’ IM-2 mission will both feature advanced lunar drills capable of collecting subsurface samples in some of the most extreme environments on the Moon. One of the key systems in these missions is the TRIDENT drill, covered in more detail later, which is specifically designed to navigate the challenges of lunar regolith, cold temperatures, and limited power. These efforts aim to demonstrate how robotic drilling can support in-situ resource utilization and pave the way for long-term lunar operations.
ESA’s PROSPECT mission will deploy the ProSEED augering drill paired with the ProSPA mini-lab. The system targets permanently shadowed polar regions where ice may exist. It uses an integrated multispectral imager and permittivity sensor to assess the regolith’s physical properties during drilling.
Once samples are extracted, they’re heated in miniature ovens to release volatiles like water vapor, which are then analyzed to support lunar ISRU (in-situ resource utilization) research.
Mars
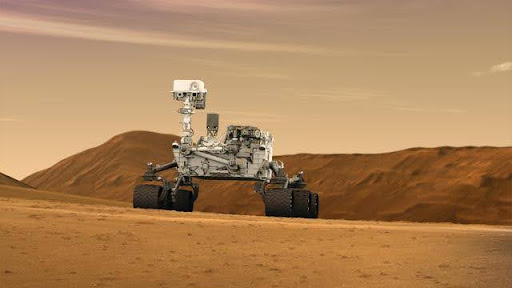
NASA’s Curiosity rover used a percussive drill to collect powdered rock samples from sedimentary outcrops. When its internal drill feed mechanism failed, engineers developed an innovative feed-extended drilling workaround, pressing the drill against the rock using the rover’s robotic arm, effectively mimicking a handheld press drill.
The Perseverance rover upgraded this technology with a rotary coring drill that extracts solid core samples, roughly 6 cm long, which are sealed in titanium tubes for eventual return to Earth. The system includes sensors to monitor drilling vibrations and drilling depth, and it uses a visual verification step to ensure successful sample capture.
ESA’s Rosalind Franklin rover (part of the ExoMars program) is set to push drilling depth limits even further, reaching up to 2 meters below the Martian surface. Its drill includes a spectrometer (Ma_MISS) embedded in the drill bit itself, designed to analyze borehole walls in real time. The instrument will study underground mineralogy and detect potential biosignatures. Unlike previous missions, this drill uses a long augering drill string with automated sampling and internal transport systems that grind, sort, and prepare soil for onboard analysis.
Asteroids
Drilling on asteroids introduces unique drilling challenges due to their extremely low gravity. Applying downward force can destabilize a spacecraft or push it away from the surface. That’s why missions like Hayabusa2 and OSIRIS-REx opted for non-contact methods: they deployed small projectiles to stir up surface material and capture the floating debris.
Future asteroid mining missions will require drill mechanisms that can anchor securely, possibly using harpoons, claws, or anchoring thrusters. These drills must also handle fragile, unconsolidated materials and avoid creating ejecta that could damage nearby structures or instruments. Engineers are experimenting with synchronized triple-arm systems or percussive penetrators that distribute force evenly while minimizing drilling vibrations.
New concepts like thermal drills (which melt or sublimate material rather than cutting) and cryogenic penetrators are being explored for missions targeting icy bodies. Such approaches could reduce debris and make drilling applications safer and more efficient in microgravity.
Overcoming the Challenges of Off-Earth Drilling
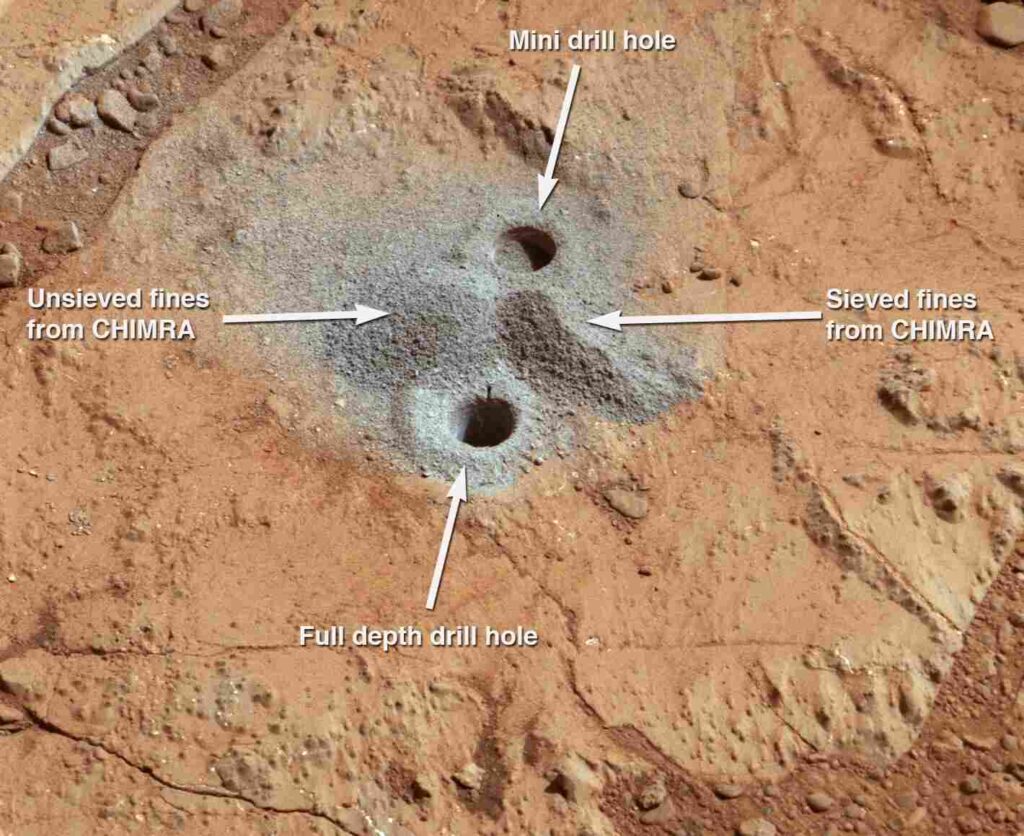
Drilling in space means adapting to extreme environmental conditions: microgravity, extreme temperature swings, variable regolith density, and limited electric power. Traditional Earth drilling systems rely on gravity, atmospheric pressure, and sometimes even external stabilizers, none of which are available on other planetary bodies.
Another factor is drilling vibrations. In microgravity, these can destabilize the entire lander or rover. Designs must account for and mitigate vibrations through damping materials or synchronized dual-drill systems, especially on small bodies like asteroids, where anchoring is difficult.
Energy efficiency is also critical. With limited solar exposure and battery capacity, drills must conserve drilling power and optimize power consumption. Many rely on low-torque, high-efficiency motors paired with intelligent software. Some systems are now experimenting with real-time adjustment based on ground resistance, powered by onboard artificial intelligence to adapt to unpredictable subsurface materials.
Then there’s the issue of clearing debris. On Earth, drilling fluids help flush out cuttings, cool the bit, and stabilize the borehole. But in space, these fluids would instantly evaporate or freeze. So engineers turn to dry solutions: fluted drill bits that channel cuttings out, rotating brushes that sweep material aside, and collection chambers that isolate samples for testing.
Together, these innovations form the backbone of a new generation of drilling techniques, designed specifically for off-earth drilling in places where gravity can’t help and failure isn’t an option.
Next-Gen Tech: Honeybee Robotics’ TRIDENT
Honeybee Robotics is leading the charge in drilling applications for space. Their TRIDENT drill that we’ve mentioned above, is one of the most advanced tools for robotic drilling campaigns. It’s designed to work in Moon-like conditions: dusty, cold, and nearly airless. TRIDENT is a rotary-percussive drill, spinning and hammering simultaneously. This dual action is perfect for cutting through highly compacted lunar regolith, which can be as hard as concrete.
The system is designed to minimize power consumption while maintaining high drilling performance, and it includes sensors that collect temperature and resistance data with every bite it takes. These measurements help scientists model subsurface thermal conductivity and moisture distribution below the lunar surface.
TRIDENT also uses a bite sampling strategy, drilling in ~10 cm increments and withdrawing between each cut to prevent clogging and overheating. It features fluted drill bits to transport cuttings upward, and a rotating brush to sweep them toward the MSolo spectrometer for volatile analysis. As it drills, it can operate in extreme cold (down to -150°C), thanks to built-in heaters and sensors that prevent frost buildup and bit freezing.
Already tested on Earth and set to fly aboard NASA’s VIPER rover, TRIDENT represents the future of drilling performance in space, combining smart design, rugged components, and a mission-focused approach.
The Future Beneath the Surface
Space drilling is more than a technical achievement; it’s becoming a foundation for future exploration. As tools improve and missions grow bolder, every borehole brings us closer to sustainable off-Earth living. What we learn underground may well determine how far and how long we go.
Want to dig deeper into the future of drilling in Space? Keep an eye on missions like VIPER, ExoMars, and the next wave of asteroid mining companies. They’re literally breaking new ground.