For decades, assembling anything in space meant shipping every single part from Earth. However, the future of space exploration requires more than rockets filled with spare parts. It calls for a paradigm shift: building what we need, where we need it. That’s where 3D printing in space comes in.
Also called additive manufacturing, this method creates objects layer by layer, using a material for 3D printing like metal, plastic, or even Lunar regolith. From printing critical components in orbit to shaping structural components out of Martian soil, 3D printing technology is poised to revolutionize how we survive, build, and thrive in space.
Why Print Instead of Ship?
Launching gear into space is incredibly expensive. The cost to deliver just one kilogram of payload into orbit can reach tens of thousands of dollars. That’s where manufacturing in space changes everything. Instead of sending entire spacecraft components from Earth, astronauts could print what they need using local raw material or feedstock delivered in bulk.
This shift does more than just save money:
- It reduces launch costs and frees up precious cargo space.
- It supports long missions by printing tools, spare parts, or even medical supplies on demand.
- It unlocks the possibility of human presence beyond low Earth orbit by creating landing pads, habitats, and blast walls directly on planetary surfaces.
As NASA explains, this strategy addresses the most pressing challenges of space exploration: resupply limitations, risk of failure, and mission flexibility.
Building on the Moon and Mars: From Dust to Shelter
Perhaps the most exciting application of 3D printing in space is building with what’s already there. Scientists and engineers are developing printers capable of using Lunar regolith or Martian regolith as feedstock. These materials – essentially space dirt – are rich in silicates, oxides, and other minerals that can be transformed into solid construction materials using sintering or binder-based techniques.
This concept is no longer theoretical. NASA has awarded a $57.2 million Phase III Small Business Innovation Research (SBIR) contract to construction firm ICON to advance its Olympus construction system. The project, which extends through 2028, will focus on developing 3D printing technologies that use local materials like lunar and Martian regolith for building infrastructure, including habitats, roads, and landing pads.
The award builds on ICON’s earlier dual-use contract with the U.S. Air Force, co-funded by NASA, and marks a significant step toward creating a sustainable lunar presence
The resulting material is often referred to as Lunarcrete – a Moon-made analogue of concrete. It supports highly durable, autonomous construction that withstands the environment of space.
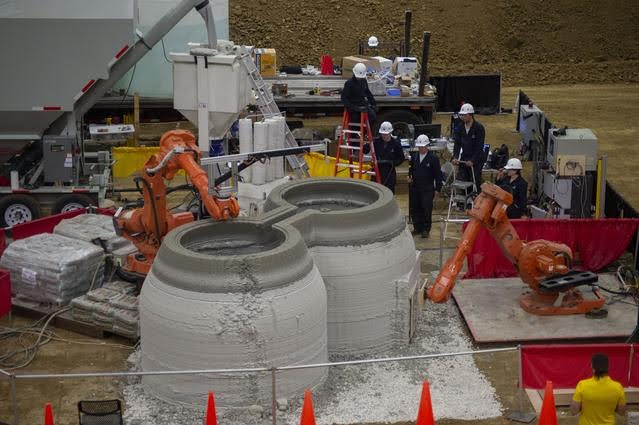
Key benefits include:
- Using local raw material, thus eliminating the need to ship bulky supplies.
- Improving structural integrity in structures exposed to Moonquakes and micrometeorites.
- Offering high heat resistance against solar radiation and thermal extremes.
- Enabling innovative designs through the flexibility of the 3D printing process, such as domes and modular walls.
Recent ESA trials have even demonstrated solar sintering, where focused sunlight fused regolith into solid bricks – a sustainable approach to construction with no added binders.
Printing in Orbit: Smarter, Faster, Safer
The International Space Station (ISS) has served as a testing ground for 3D printing services in microgravity. Since 2014, NASA’s Additive Manufacturing Facility (AMF) has produced plastic tools and experimental parts on demand.
More recently, in 2023, the ESA’s Metal 3D Printer aboard the ISS successfully printed the first metal object in orbit using stainless steel wire. The component, once returned to Earth, was tested for strength and structure, marking a milestone for 3D metal printing.
Being able to print components in space is a major step forward. It reduces reliance on cargo missions and allows astronauts to fabricate tools, connectors, or critical components on the spot. NASA’s long-standing work with Made In Space and Redwire has shown that in-space manufacturing is viable, safe, and versatile.
NASA is also testing advanced methods like electron beam melting, which uses focused energy beams to fuse metal powder, forming parts layer by layer with highly controlled mechanical properties and complex geometries ideal for use in spacecraft or station maintenance.
Space Mining Meets 3D Printing
So, how does this connect to space mining? Mining for resources on asteroids, the Moon or Mars isn’t just about extraction but about sourcing the raw materials needed for 3D printing structures, tools, and equipment directly in space. And this is where 3D printing technology becomes a key enabler.
Instead of hauling mined material back to Earth, we can process and reuse it on-site to produce essential aerospace industry components through additive manufacturing. Some practical examples include:
- Metal-rich asteroids could provide feedstock for 3D metal printing, producing tools, brackets, and frames.
- Extracted regolith or minerals can be processed into material for 3D printing for construction or manufacturing.
- In-situ fabrication of spacecraft components, shielding, and structural supports for mining equipment or habitats becomes feasible.
According to ESA, regolith-based bricks can be sintered using solar energy, allowing infrastructure to be built with just dust and concentrated sunlight – a breakthrough in energy-efficient additive manufacturing.
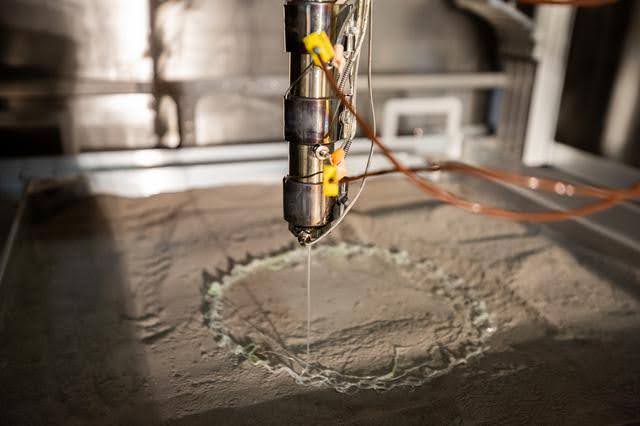
NASA and AI SpaceFactory test 3D printing with regolith simulant in a lunar-like vacuum at Kennedy’s Swamp Works (REACT project, 2022).
Together, space mining and 3D printing are laying the groundwork for a future of space exploration, and possible habituation, where we build directly with what we extract, supporting sustainability, autonomy, and long-term human presence in space.
The Power of Advanced Manufacturing
Operating in space means facing not just extreme challenges, but constant uncertainty. That’s why flexibility is key. Advanced manufacturing allows for rapid prototyping and printing technology that adapts to mission needs.
Some of the biggest advantages include:
- Fabrication of parts with complex geometries that are impossible with casting or machining. This allows engineers to design lightweight, intricate structures like heat exchangers or satellite brackets optimized for space use.
- Improved mechanical properties tailored to the space environment. Additive manufacturing enables control over internal structure and density, enhancing strength, flexibility, or heat resistance based on specific mission demands.
- Customization of parts for specific mission phases or emergencies. If a unique tool or structural fix is needed, astronauts can fabricate it on-site instead of relying on Earth-based resupply.
With additive techniques, we can even print parts with varied material properties in a single build. For example, a component might need to combine rigidity and flexibility in different regions, which is ideal for dynamic systems.
What Lies Ahead
Looking ahead, 3D printing is expected to become a foundational tool for long-duration space missions. With NASA’s Artemis program and ESA’s ISRU efforts pushing the boundaries of off-world construction, the technology is rapidly moving from experiment to necessity.
In the years ahead, 3D printing services will likely expand beyond human crews to support robotic systems, space mining, and satellite repair, making it an essential part of building sustainable operations in space. It’s not just about going further – it’s about staying longer, building smarter, and using what space gives us to shape what comes next.